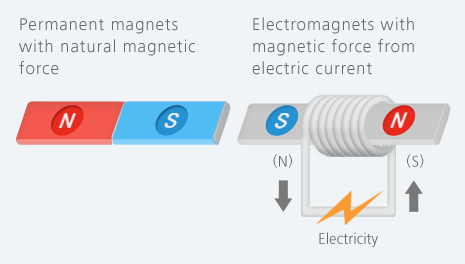
In recent times, variable-speed compressor motors have gained immense popularity as their market share has gone up due to the increase in the sale of inverter air conditioners and refrigerators. These advanced compressors exhibit improved efficiency and reliability due to upgrades in material and manufacturing technology and improved design.
In an air conditioner, the compressor is like the heart. Almost all air conditioner manufacturers do research regarding the compressor to make it more efficient in terms of performance and power savings. In today’s times of rapidly changing technology, people have started opting for inverter compressors over fixed-speed compressors in air conditioners.
The unproductive utilization of electricity to run air conditioner compressors is perceived as a secondary sponsor to the emission of greenhouse gases to the delicate environment. This emission can be controlled by enhancing the energy adaptation efficiency of air conditioners and refrigerators. One of the ways of attaining this is via capacity control, which meets the system capacity to the running load. Capacity control brings down the on/off pedalling losses of the machine and enhances the uniform-state efficiency of an air conditioner due to a lower pressure difference across the compressor at part-load situations.
How Does a Conventional Compressor Work?
The "Single Speed" principle defines the working of a conventional compressor. Given the loading or temperature setting of an air conditioner's thermostat, they remain either "ON" or "OFF." In this situation, the majority of compressors are made to withstand optimum load conditions, meaning they will run at peak load even in the winter when the outside temperature is lower.
This causes high power usage and the user pays an inflated electricity bill every month. In addition, conventional compressors are made to look after the heat ingress due to outdoor variations for air conditioners.
How Does an Inverter Compressor Work?
Contrary to the typical compressor, the inverter compressor follows the approach of ‘Variable Frequency Drive’ to make the compressor speed change as an outcome of different load conditions. These variations in the speed of the compressor make the refrigerant flow vary.
The inverter technology is the most advanced technological upgrade in regard to the compressor motor. An inverter is meant to control the speed of the compressor motor, in order to continuously control the temperature. With the use of an electrical inverter that can be adjusted, the inverter units' variable-frequency drive regulates the compressor motor's speed, which in turn modifies the compressor output.
After the drive converts the incoming alternating current (AC) supply into direct current power, an electrical inverter regulates it to develop the desired current frequency. A microcontroller gauges the temperature of the environment and adjusts the compressor's speed accordingly.
An inverter compressor helps make sure that during times of high load during the summer months, the compressor operates at its optimum capacity. In times of lesser load, the compressor adjusts its cooling capacity to save power.
Advantages with Inverter Compressors
The technology of inverter compressors is found to be extremely effective and receptive. Moreover, it is a silent, compact unit that makes space for installation flexibility. In comparison to conventional air conditioners, inverter air conditioners are more efficient. Acute variations in the load can also be eliminated. As a result, the inverter units are more dependable, quieter, and have lower operating costs. Lower energy expenses can offset the initial cost of the inverter systems, which are more costly than constant speed air conditioners.
If you are looking to buy a 1.5 ton inverter AC, you can choose Daikin’s highly energy-efficient air conditioners that are high in features and performance.